
10 Supply Chain Challenges in Automotive Industry: Post-Pandemic Resilience – The automotive industry, a complex network of manufacturers, suppliers, and distributors, has faced unprecedented challenges in recent years, especially in the aftermath of the global COVID-19 pandemic. Disruptions in the supply chain have highlighted vulnerabilities and underscored the need for resilience. In this article, we delve into the supply chain challenges facing the automotive industry and explore strategies for post-pandemic resilience.
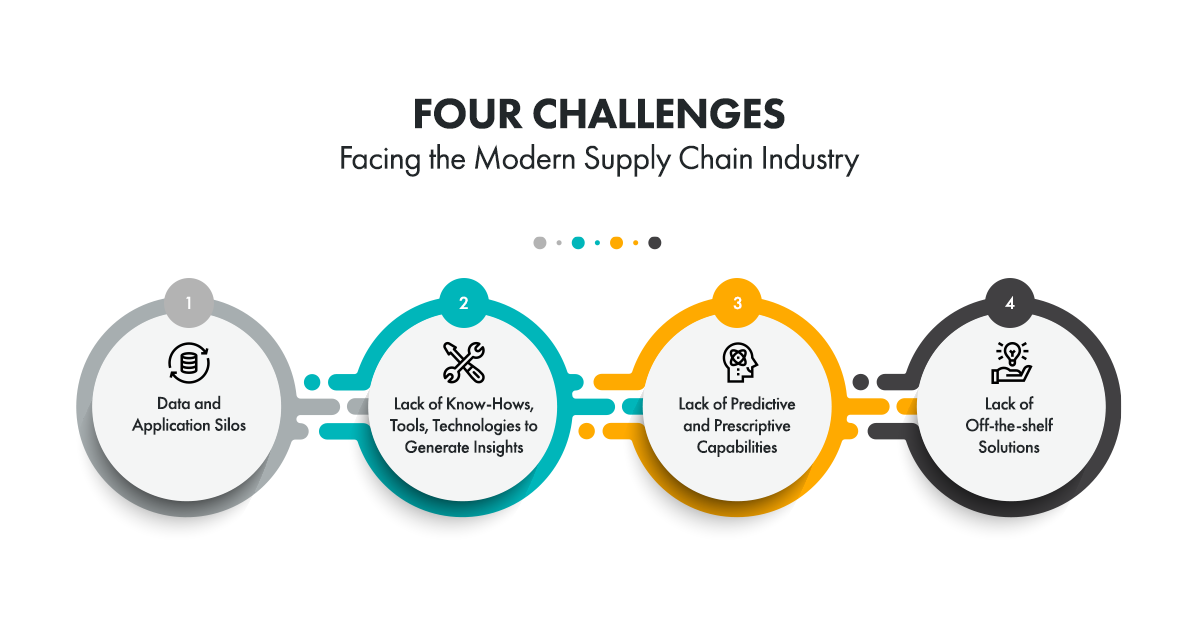
1. Global Semiconductor Shortages: Impact on Production
One of the most critical challenges in the automotive supply chain is the global semiconductor shortage. The increasing reliance on electronic components in vehicles, coupled with disruptions in semiconductor production, has led to a shortage affecting automakers worldwide. This scarcity has resulted in production delays, reduced output, and increased costs for the automotive industry.
2. Fluctuating Raw Material Prices: Cost Pressures on Manufacturers
The automotive industry is highly dependent on raw materials, and fluctuating prices present a significant challenge. Variations in the prices of materials like steel, aluminum, and plastics can impact production costs, affecting the overall profitability of automakers. The industry must navigate these price fluctuations while maintaining competitiveness in the market.
3. Supply Chain Visibility and Transparency: Addressing Complexity
The complexity of the automotive supply chain makes visibility and transparency crucial. Many automakers source components from a global network of suppliers, making it challenging to have real-time visibility into every tier of the supply chain. Lack of transparency can lead to inefficiencies, delays, and difficulties in identifying and mitigating potential disruptions.
4. Just-In-Time (JIT) Inventory Practices: Balancing Efficiency and Risk

The adoption of Just-In-Time (JIT) inventory practices, aimed at reducing costs and improving efficiency, has become a standard in the automotive industry. However, this approach leaves little room for buffer stocks, making the supply chain susceptible to disruptions. Striking a balance between JIT practices and building resilience has become a critical consideration. (Read More : Electric Vehicles EVs: Shaping the Future of Transportation in 2024)
5. Transportation Disruptions: Impact on Timely Deliveries
Transportation disruptions, including port congestion, shipping delays, and logistics challenges, can significantly impact the timely delivery of automotive components. These disruptions, often exacerbated by global events such as the pandemic, natural disasters, or geopolitical tensions, pose a constant risk to the continuity of the supply chain.
6. Cybersecurity Threats: Protecting Digital Infrastructure
As the automotive industry becomes more digitally connected, the risk of cybersecurity threats to the supply chain increases. Malicious attacks on digital infrastructure, including manufacturing systems and communication networks, can disrupt operations and compromise sensitive data. Implementing robust cybersecurity measures is essential for safeguarding the integrity of the supply chain.
7. Sustainability and Environmental Regulations: Shaping Supply Chain Practices
Increasing emphasis on sustainability and stringent environmental regulations are reshaping supply chain practices in the automotive industry. Automakers must navigate evolving standards, source environmentally friendly materials, and adopt sustainable manufacturing processes, adding complexity to the supply chain.
8. Geopolitical Instability: Impact on Global Supply Chains
Geopolitical instability, trade tensions, and policy changes can have a profound impact on global supply chains. Automotive manufacturers are particularly vulnerable to shifts in geopolitical dynamics, as they often rely on components sourced from different regions. Navigating geopolitical uncertainties is a critical aspect of ensuring supply chain resilience.
9. Talent Shortages and Skill Gaps: Building a Competent Workforce
The automotive industry faces challenges related to talent shortages and skill gaps, especially in areas such as digitalization, data analytics, and cybersecurity. Building a competent workforce equipped to handle the complexities of a modernized supply chain is essential for overcoming challenges and driving innovation.
10. Collaboration and Digitalization: Key Strategies for Resilience
In the post-pandemic era, collaboration and digitalization have emerged as key strategies for enhancing supply chain resilience in the automotive industry. Collaborative relationships with suppliers, leveraging advanced technologies such as artificial intelligence, blockchain, and data analytics, can improve visibility, streamline processes, and proactively address disruptions.
Conclusion article 10 Supply Chain Challenges in Automotive Industry: Post-Pandemic Resilience
In conclusion, the automotive industry faces multifaceted challenges in its supply chain,* and the path to resilience involves a holistic approach. From addressing semiconductor shortages to embracing digitalization and fostering collaboration, automakers must adapt to a rapidly evolving landscape. Post-pandemic resilience requires a proactive stance, a commitment to innovation, and the flexibility to navigate an ever-changing global environment. As the industry continues to recover from disruptions, the lessons learned during challenging times will shape the strategies employed to build a more resilient and robust automotive supply chain for the future.
Read More : Digital Transformation in Automotive Retail: Online Sales and Virtual Showrooms
2 thoughts on “10 Supply Chain Challenges in Automotive Industry: Post-Pandemic Resilience”
Comments are closed.